Exhaust gas cleaning using ceramic catalytic filter systems
Removes particles, acidic gases, and nitrogen oxides (NOx) in a single system unit. Often requires less installation space compared to conventional, separate systems.
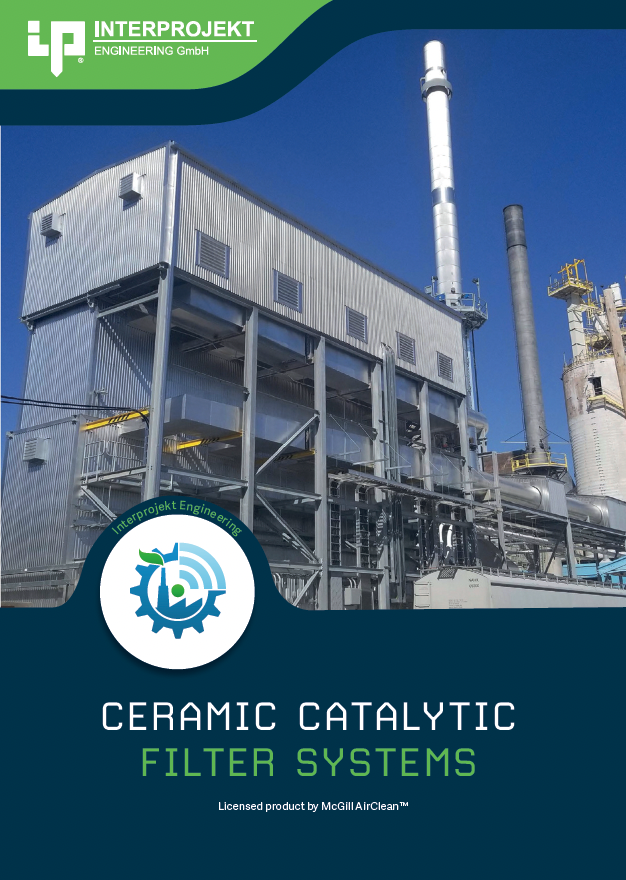
Operation of the catalytic candle filter system
Particle Separation:
As the flue gas passes through the ceramic filters, the remaining particles are collected on the outer surface of the filters. The cleaned flue gas flows upwards through the filter candles and exits through an opening. The filter candles are periodically cleaned with compressed air.
Separation of Acidic Components:
Dry alkaline reagent is pneumatically injected into the flue gas channel before the catalytic filter, where acidic components react with the alkali to form solid particulate salts. The reacted salts and unreacted alkali accumulate on the outer surface of the catalytic filters, forming a dust cake. This dust cake provides a secondary reaction site for the unreacted alkali to further react with additional acidic components.
Denitrification:
Ammonia or urea is introduced into the flue gas channel before the catalytic filter. The catalyst present in the ceramic filters drives the reaction between the ammonia or urea reagent and the nitrogen oxides (NOx).
Advantages of the Interprojekt ceramic catalytic filter systems:
1. Modular construction and 100% availability:
Our ceramic catalytic filters consist of at least three modules, with the ability to take one module offline during operation. The remaining modules can temporarily handle the entire exhaust gas flow, allowing for candle replacement or maintenance without the need to switch the filter system to bypass mode.
2. Optimized airflow to the ceramic catalytic filter
We equip each module with baffles instead of conventional perforated plates or diffusers, ensuring that the flue gas is evenly distributed throughout the module. Uneven gas distribution can result in frequent filter cleaning, excessive wear, and a high degree of particle entrapment, which may lead to premature filter failure.
3. Gas Velocity and Distribution :
We do not dimension our systems solely based on the “air-to-cloth ratio”; we also take the system’s “can velocity” into account. When the internal velocities in the ceramic catalytic filter and the bypass velocity across the surface are too high, frequent filter cleaning, excessive wear, and high particle entrapment can lead to premature filter failure. By ensuring sufficient spacing between the filter candles, we reduce the gas velocity around them to an acceptable level, thereby increasing the lifespan of the ceramic catalytic filter.
4. Easy Maintenance:
Filter inspection and replacement are the most critical and time-consuming maintenance operations performed on a catalytic filter system. To inspect and service the filters properly, the module design must provide easy access to the filters and must provide easy access to the filters and a safe work environment for maintenance personnel. Our catalytic filters are designed so maintenance work can be done from the outside of the module, free from exposure to particulate and flue gas.
With our long-term partner and licensor for candle filters McGill AirClean, we have had catalytic candle filters in our portfolio since 2021.View of a typical catalytic filter:
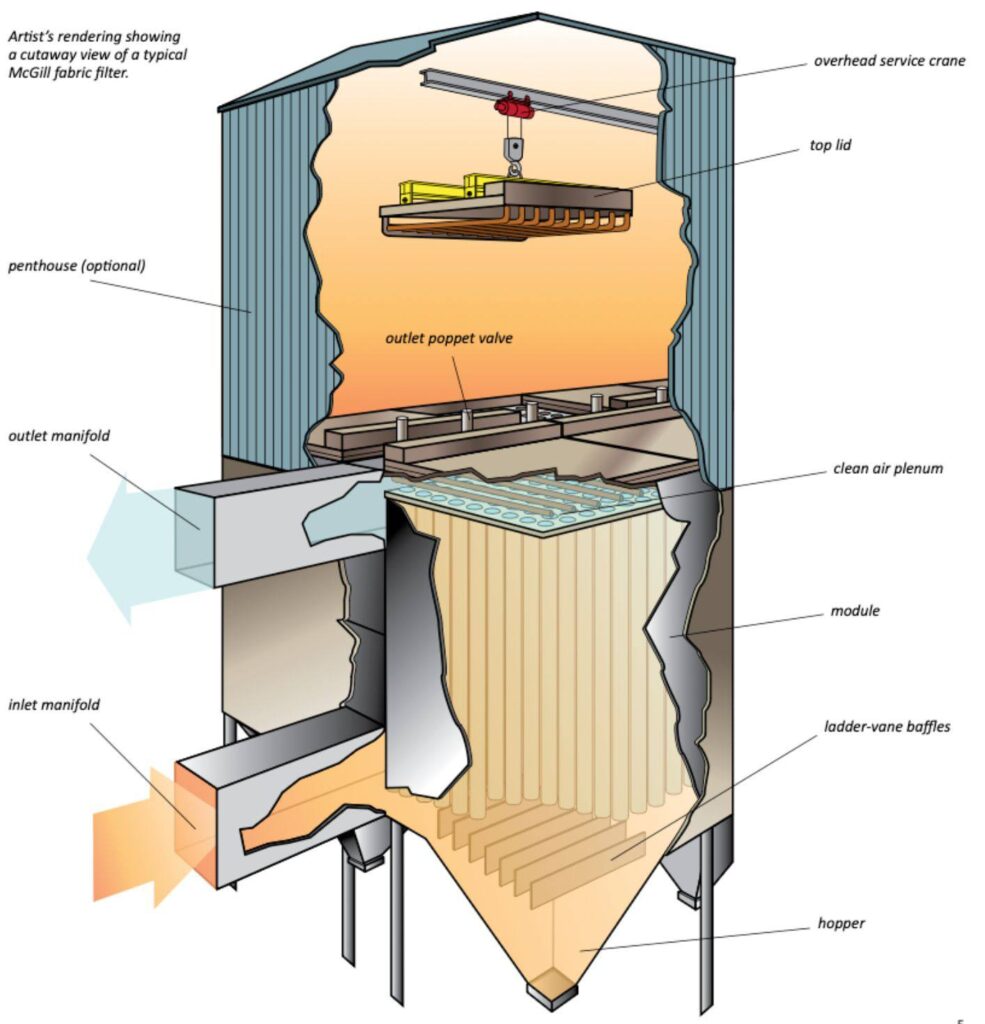
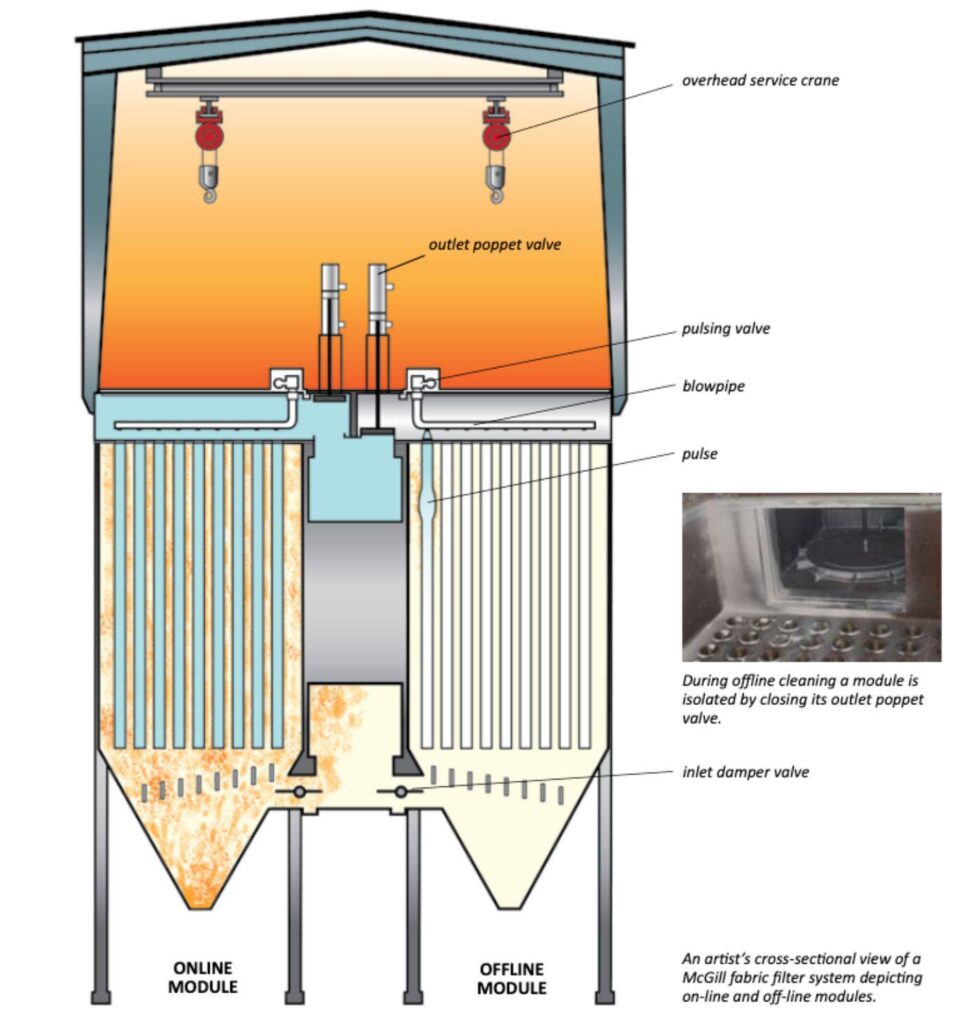
All information is also available as a PDF download.:
Ceramic Catalytic Filter Systems (englisch)
katalytische keramische Kerzenfilter (german)
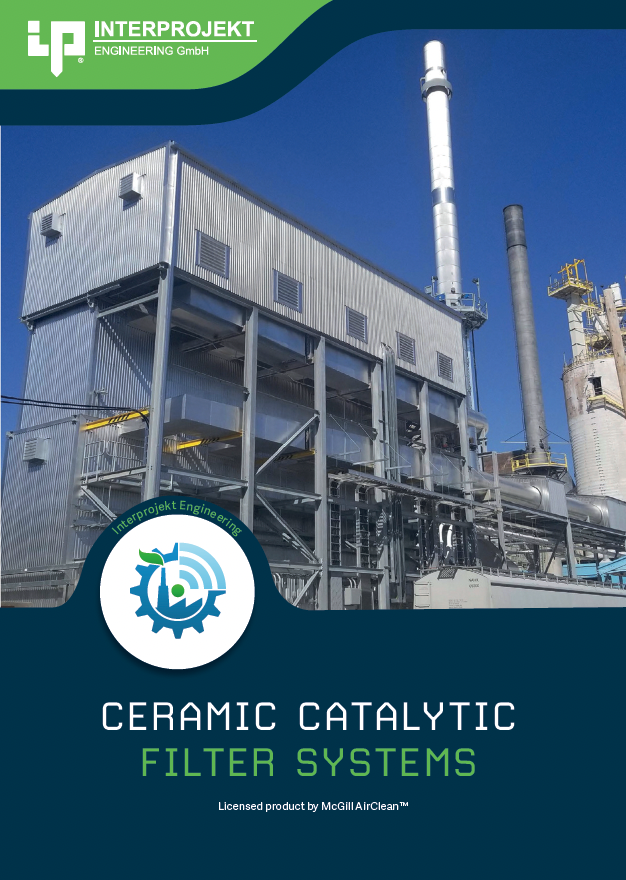